Everything you need to know about ignition coil charge-up
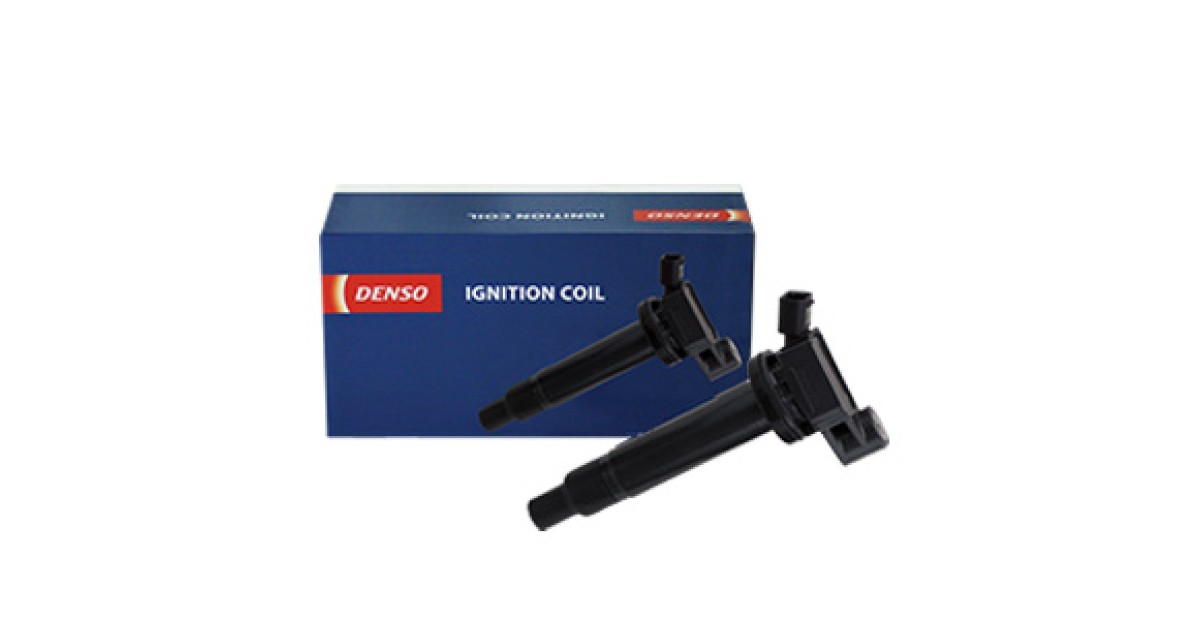
Published4 January 2022
When working with mechanical ignition systems, it’s crucial to understand ignition coil charge-up and dwell time. This guide will give you everything you need to know about how charge-up works for different ignition systems and engine speeds – and how common ignition problems can arise.
What is coil charge-up?
When an electric current is applied to the primary winding of an ignition coil, it will take a short time for the current flow to reach its maximum amperage. Therefore – because the strength of the magnetic field (or magnetic flux) created around the winding is directly proportional to the current flow – it will also take the same amount of time for the magnetic field to reach its maximum strength. When the current flow and magnetic field are at their maximum, the magnetic field will then be stable.
The time taken to build the magnetic field to maximum strength is often referred to as the ‘charge-up’ time for the ignition coil.
There are two potential issues this presents:
- If the electric current is not applied to the primary winding for long enough, the magnetic field will not reach its maximum strength;
- If the current is applied for too long, it could cause overheating of the electrical circuits and the primary winding.
How long does a coil take to charge up?
The required charge-up times vary with different types of ignition coil, but are typically in the range of 4 milliseconds for older ignition coils down to approximately 1.5 milliseconds for many modern coils.
The period when the ignition system applies an electric current to the ignition coil’s primary winding is often referred to as the “dwell period” or “dwell time”. With modern ignition systems, the dwell period is controlled electronically so there is always sufficient time to fully charge the coil. But for older mechanical ignition systems, the limitations of the mechanically operated contact breaker switch actually created a dwell time that reduced as the engine speed increased. Therefore, at higher engine speeds, the reduced dwell time prevented the magnetic field from reaching full strength.
What problems can short dwell times cause in a mechanical ignition system?
The accuracy of the ignition timing on mechanical ignition systems is limited to the capabilities of the hardware. Fine-tuning, adjustments and component replacements were often required as part of routine maintenance. As an example of the limitations, (Figure 1) shows the typical engine speed-related timing for a mechanical ignition system compared to the ideal timing.
Figure 1: A centrifugal advance mechanism isn’t able to precisely match the ideal timing
Due to the use of progressive return springs (Figure 2), the timing advance provided by the centrifugal system increases in two linear steps. However, the ideal timing advance changes in a non-linear progression. The centrifugal timing must be set carefully to ensure the ignition timing is never over-advanced.
Figure 2: The inner workings of a mechanical advance mechanism
What is the difference between dwell period and dwell angle?
On a mechanical ignition system, the dwell period starts when the rotating cam-lobes allow the contact breaker switch to close, so current flows through the coil’s primary winding. The dwell period then stops when one of the cam-lobes forces the contact breaker switch to open again, which switches off the current flow to the primary winding. The dwell period therefore depends on the angle of rotation of the cam-lobes whilst the contact breaker switch is in the closed position.
(Figure 3) shows four cam-lobes (for a four-cylinder engine), which means there will be 90° between the same points of adjacent cam-lobes. The shape of the cam-lobes in the example allows the contact breaker switch to remain closed for 60° of rotation. Therefore, there is a dwell angle of 60 distributor degrees when the contact breaker switch is closed and current flows through the coil primary winding.
Figure 3: With 90° between cam lobes, there is a 60° window in which the contact breaker switch is closed
Example 1
A crankshaft is rotating at 1,000 RPM. The distributor rotor, which rotates at half engine speed, will rotate at 500 RPM. At this speed, it will take 20 milliseconds for the distributor shaft to rotate through the 60° of dwell angle. The ignition coil requires around 4 milliseconds of charge-up time. Therefore, there is more than sufficient dwell time for the magnetic field to build up in the coil.
If the engine is rotating at 5,000 RPM, the same 60° of distributor shaft rotation will only take 4 milliseconds, which is exactly the right amount of time to charge the coil with a maximum strength magnetic field. If the engine rotates any faster than this, there will be insufficient time to fully charge the ignition coil, which will result in reduced energy in the magnetic field and reduced voltage being delivered to the spark plugs.
The problem of dwell time reducing as engine speed increases becomes more significant for engines with more cylinders.
Example 2
On a six-cylinder engine, there will be six cam-lobes, with only 60° between each lobe (Figure 4) and only 40° for the dwell angle. At an engine speed of 5,000 RPM, the 40° of dwell angle will only last for 2.6 milliseconds. If the coil requires 4 milliseconds to fully charge, then the dwell time will be too short, resulting in a lower voltage and potential misfires.
Figure 4: With six cam lobes, there is only a 40° dwell angle
Different solutions were used on mechanical ignition systems to overcome the problem of reducing dwell time. One solution was to use a more powerful ignition coil. Another extreme solution, for high-revving engines with eight or twelve cylinders, was to fit two separate distributors, each with their own ignition coil. The engines therefore effectively had two separate ignition systems, each delivering the high voltage to the spark plugs for half of the engine’s cylinders.
How does this relate to modern ignition systems?
Mechanical systems help us understand the development of the current digital ignition systems.
The one critical part of the petrol engine ignition system that has never been replaced, and probably never will be, is the spark plug.
It is critical that the spark plug provides high performance and precisely timed ignition. DENSO understands that high quality is required to meet these demands from engine manufacturers. To achieve this, DENSO combines the best and proven quality systems with years of experience.